The continuous casting tundish plays a pivotal role in modern steel production, ensuring smooth molten metal flow and optimizing the quality of the final steel product. As one of the core components in the continuous casting process, the continuous casting tundish is an intermediary vessel that connects the ladle with the mold. This device is responsible not only for the steady distribution of molten steel but also for its temperature regulation, impurity removal, and flow control during casting. In this article, we will delve into the technical aspects, engineering parameters, and operational significance of the continuous casting tundish while incorporating industry insights from renowned companies such as HANI TECH.
Introduction to the Continuous Casting Tundish
The continuous casting tundish is more than just a transitional container in the casting line; it is an essential piece of equipment that has evolved with advances in metallurgical engineering. During continuous casting, molten steel is transferred from the ladle into the mold. However, before entering the mold, the steel travels through the tundish where it is homogenized, and non-metallic inclusions are allowed to float to the top and be skimmed off. This process is fundamental in ensuring a consistent temperature and chemistry of the steel, thus leading to enhanced product quality.
In modern steelmaking environments, the importance of the continuous casting tundish cannot be overstated. Its design directly impacts the efficiency, safety, and environmental aspects of the entire steel production process. Many operators in the industry have come to recognize that optimizing the performance of the continuous casting tundish leads to reduced casting defects and improves the overall yield. Furthermore, this equipment plays an integral role in achieving the smooth metal flow essential for preventing turbulence, which can lead to undesirable inclusions and cast defects.
Role in Steel Production
In the realm of steel manufacturing, the continuous casting tundish is indispensable. It acts as a buffering vessel that mitigates fluctuations in molten steel temperature and composition. A well-designed continuous casting tundish not only guarantees smooth metal flow during casting but also provides ample residence time for the inclusions to separate. This effectively results in improved metallurgical quality and consistency in the final product.
One of the key functions of the continuous casting tundish is to facilitate the transition between the ladle and the mold. By managing the flow of molten steel, it ensures that the metal is evenly distributed, which is critical for maintaining the structural integrity of the steel. In addition, the tundish design incorporates features like flow control devices, weirs, and filters that work collaboratively to remove slag and other impurities. This is particularly important in continuous casting operations where even minor fluctuations in temperature or chemistry can negatively affect the product.
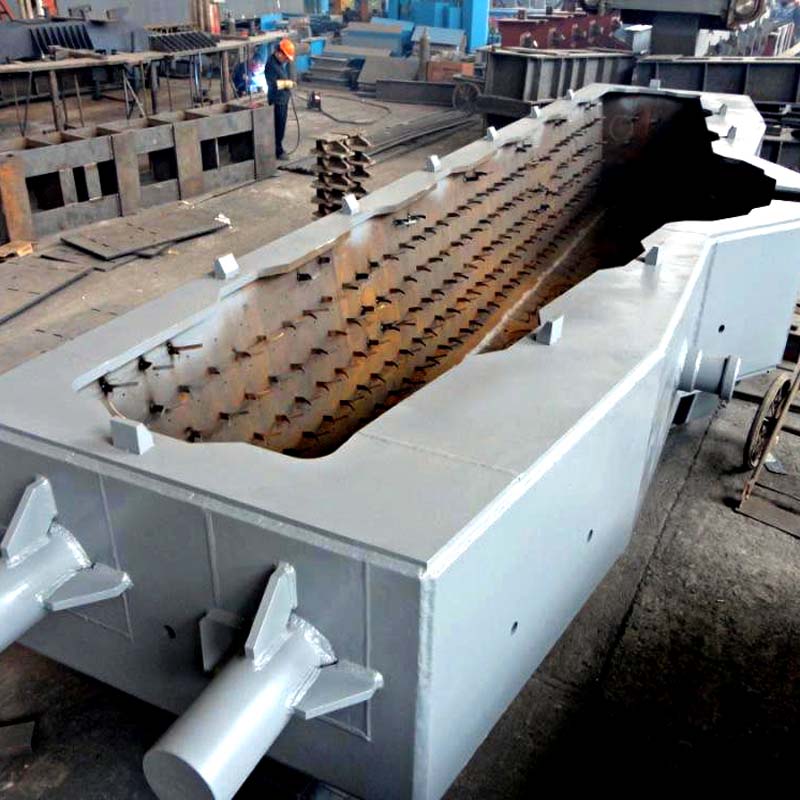
Technical Parameters and Design Considerations
The performance of the continuous casting tundish heavily depends on its engineering design and operational parameters. Advanced design techniques and computational fluid dynamics (CFD) simulations are commonly employed to optimize the shape, size, and internal structure of the tundish. This ensures that the molten steel has sufficient dwell time to stabilize before entering the mold.
Below is a detailed table summarizing various technical parameters associated with a high-performance continuous casting tundish. These parameters not only assist engineers in fine-tuning the equipment for specific steel grades but also serve as benchmarks for industrial quality and efficiency.
Parameter | Description | Typical Value | Unit | Comments |
---|---|---|---|---|
Tundish Capacity | Molten steel holding capacity between ladle and mold | 5 – 20 | Tons | Varies with production scale |
Temperature Differential | Temperature drop across the tundish | 10 – 30 | °C | Ensures proper metal solidification rate |
Residence Time | Total time molten steel stays within the tundish | 60 – 180 | Seconds | Balances flow and quality stabilization |
Flow Rate Control | Adjustable flow rate settings for controlled pour | 10 – 50 | Liters/second | Depends on casting speed |
Surface Area | Exposure area for slag skimming | 20 – 50 | m² | Larger area improves slag removal |
Cooling Capacity | Efficiency of tundish cooling system | High Efficiency | N/A | Critical for minimizing heat loss |
Flow Distribution Plates | Internal plates used to direct steel flow | Configurable | N/A | Ensures laminar flow |
Stirring Mechanism | Oscillatory or electromagnetic stirring methods | Variable | N/A | Improves temperature homogenization |
Refractory Lining Thickness | Protective lining material thickness | 50 – 150 | mm | Depends on steel grade and operation temperature |
Bypass Channel Design | Design features for diverging the flow if necessary | Optimized per design | N/A | Minimizes casting disturbances |
Inclusion Removal Efficiency | Percentage removal of non-metallic inclusions | 80 – 95 | % | Critical quality control parameter |
Oxygen Activity Control | Management of oxygen content in the molten steel | Tight Control | N/A | Prevents oxidation and defects |
Operational Temperature Range | Temperature operating limits for safe function | 1400 – 1600 | °C | Covers most carbon steel productions |
Automation Level | Integration of automatic control systems | High | N/A | Ensures reproducibility and safety |
Maintenance Interval | Time between scheduled maintenance checks | 200 – 300 | Hours | Based on operating conditions |
Advanced Design Features and Operational Benefits
Over the past decades, continuous casting tundish designs have incorporated several advanced features that have revolutionized the steel casting process. Modern designs integrate computer-aided design (CAD) and CFD simulations to optimize each component of the device. This engineering approach ensures that the continuous casting tundish delivers a near-ideal flow pattern with minimal turbulence. The optimized flow results not only help in controlling the temperature gradients but also in reducing oxidation and preventing the entrapment of impurities.
One of the innovative improvements in tundish design is the incorporation of adjustable flow control devices. By enabling operators to modulate the molten steel flow, these devices ensure that the molten metal enters the mold at a consistent rate, thus reducing the risk of defects such as cracks and segregation. Moreover, some continuous casting tundish systems now include electromagnetic stirring, which further promotes the homogeneity of the molten steel. This not only improves the mechanical properties of the final cast product but also increases the efficiency of the subsequent hot rolling processes.
Companies like HANI TECH have been at the forefront of integrating advanced technological solutions into steel production. By leveraging their experience with hot rolling mills, as showcased on their website (HANI TECH Hot Rolling Solutions), and their pioneering work with various metallurgical furnaces (HANI TECH Metallurgical Furnaces), they have provided comprehensive systems where the continuous casting tundish is harmoniously integrated into an overall process optimization strategy. This integration ensures that the transition from molten steel to rolled product is seamless, efficient, and of the highest quality.
Impact on Production Efficiency and Product Quality
The critical function of the continuous casting tundish extends beyond mere transfer of molten metal. Its impact is deeply felt in overall production efficiency and product quality. A well-designed tundish minimizes temperature fluctuations and turbulence, which are common culprits in casting defects. By controlling these factors, the continuous casting tundish ensures that the steel’s microstructure remains consistent—a critical consideration when high-quality steel is required for demanding applications in construction, automotive, and heavy machinery industries.
Furthermore, the continuous casting tundish is engineered to allow for secondary metallurgy processes to take place. For instance, elements such as oxygen activity can be adjusted, and inclusions removed, prior to filling the mold. Such control steps are indispensable in achieving superior metallurgical characteristics, such as improved toughness and fatigue resistance in the final product.
The design of the continuous casting tundish also incorporates robust refractory linings that stand up against the extreme temperatures and chemical activity of molten steel. With a proper refractory design, the tundish maintains its structural integrity over long periods of operation, thereby reducing the frequency of costly maintenance shutdowns and enhancing plant uptime. This is one of the multiple reasons why the continuous casting tundish remains an economically attractive option within modern steelmaking operations.
Integration with Modern Automated Systems
In today’s competitive steel industry, automation is no longer a luxury but a necessity. Modern continuous casting tundish systems incorporate advanced sensors and automated control systems. These innovations enable real-time adjustments in flow rate, temperature control, and composition monitoring. Data from these systems can be directly fed into plant-wide control centers, allowing for immediate corrective measures should any deviations be detected during casting.
Automated continuous casting tundish systems contribute significantly to operator safety by reducing the need for manual oversight in hazardous high-temperature environments. In addition, automation plays a critical role in ensuring consistent quality and performance. The integration of these advanced systems has been shown to improve energy efficiency and reduce overall production costs, making the continuous casting tundish not only a technical necessity but also an economically sound investment.
Operational Challenges and Maintenance Strategies
Although the continuous casting tundish is a highly advanced piece of equipment, maintaining its optimal operation does pose certain challenges. One of the primary concerns is the management of refractory wear. Over time, the harsh environment inside the tundish can lead to degradation of the refractory lining, potentially compromising performance. Regular inspection and maintenance are essential to ensure that the tundish continues to function within the required parameters.
Operators must also monitor the functioning of flow control devices and stirring mechanisms. Deviations from the expected performance can result in temperature anomalies or turbulent flow, which can ultimately lead to casting defects. To mitigate these issues, many steel mills implement predictive maintenance techniques based on data analytics. By analyzing historical data and current sensor readings, maintenance teams can schedule timely interventions, thereby minimizing downtime and production disruptions.
Additional operational challenges include ensuring that the tundish’s cooling system performs efficiently, particularly during high-output periods. The cooling mechanisms must rapidly dissipate heat to prevent localized overheating, which could destabilize the flow and temperature control. Here again, the continuous casting tundish’s proper design and the integration of automated monitoring systems are vital.
Case Studies and Industry Applications
The continuous casting tundish has been successfully implemented in various steel production facilities around the world. For example, several modern plants have reported a significant reduction in casting defects after upgrading their tundish systems with advanced flow control and secondary metallurgy features. In these cases, the improvements in molten steel quality have led to savings in downstream processing, including hot rolling and finishing operations.
One notable case involved a steel plant that integrated an advanced continuous casting tundish with enhanced electromagnetic stirring and automated temperature controls. This integration not only improved the consistency of the cast slabs but also increased the overall throughput of the plant. The results demonstrated superior mechanical properties in the finished product, increased production efficiency, and reduced energy consumption. Such success stories highlight the transformative impact that a well-engineered continuous casting tundish can have on the entire steel production lifecycle.
Furthermore, insights gleaned from collaboration with companies like HANI TECH show that combining the strengths of advanced hot rolling mills and metallurgical furnaces with an optimized continuous casting tundish can bring about a new era of production excellence. The synergy between these systems results in a streamlined process where each component—from the tundish to the final rolling mill—is finely tuned for quality and efficiency.
Future Trends and Technological Innovations
Looking ahead, the evolution of the continuous casting tundish is expected to continue as the steel industry pushes towards greater automation, improved energy efficiency, and even higher product quality. Research and development in the areas of refractory materials, sensor technology, and CFD-based optimization are anticipated to further improve the performance of the continuous casting tundish.
One emerging trend is the application of artificial intelligence (AI) and machine learning (ML) in the monitoring and control of continuous casting systems. By leveraging vast amounts of operational data, AI algorithms can predict potential failures or deviations in real time and suggest corrective actions. This level of predictive maintenance and process optimization will likely drive the next generation of continuous casting tundish designs.
Additionally, improvements in environmental controls and energy recycling methods are expected to have a significant impact on the design of continuous casting tundish systems. Enhanced insulation materials and more efficient cooling strategies will play key roles in reducing the carbon footprint of steel production—a goal that is increasingly important as global environmental standards become more stringent.
Conclusion
In summary, the continuous casting tundish is an indispensable element in the modern steel production process. With its multifaceted role—from ensuring smooth metal flow and temperature uniformity to removing impurities and facilitating automation—the continuous casting tundish contributes significantly to the efficiency, safety, and quality of steel manufacturing. Through optimized design, rigorous control of operational parameters, and the incorporation of advanced technologies, this equipment continues to push the boundaries of what is achievable in the field of metallurgy.
Industry leaders like HANI TECH have demonstrated that the integration of a well-engineered continuous casting tundish with cutting-edge hot rolling and metallurgical furnace technologies is key to achieving production excellence. As the steel industry evolves, continuous improvements in the design and operation of the continuous casting tundish will remain a central focus, ensuring that steel plants can meet the ever-increasing demands for quality, efficiency, and environmental performance.
Ultimately, understanding and implementing the best practices for deploying the continuous casting tundish can revolutionize the casting process. With its optimal control of molten steel flow and temperature, this core equipment sets the stage for a successful and sustainable steel production environment. As research and technology drive further innovation, the continuous casting tundish will undoubtedly continue to be a crucial enabler in the advancement of steelmaking practices worldwide.
The continuous casting tundish, therefore, stands as a testament to the integration of advanced engineering and practical metallurgy. By focusing on robust design features, precise operational control, and a commitment to continuous improvement, modern steel plants are well-equipped to meet the challenges of tomorrow’s steel production demands.