The electric arc furnace (EAF) is a cornerstone of modern metal production, known for its efficiency and flexibility. Central to the operation of an EAF is the electric arc furnace flue, a critical component that plays a significant role in managing emissions and enhancing sustainability. This article explores the latest innovations in electric arc furnace flue technology, emphasizing their importance in eco-friendly metal manufacturing processes.
Understanding Electric Arc Furnace Flues
Electric arc furnace flues are designed to capture and manage gases produced during the melting process. These flues are essential for minimizing environmental impact, as they help reduce harmful emissions and improve energy efficiency. The advancements in flue technology are pivotal in supporting the industry’s shift towards sustainable practices.
Key Innovations in Electric Arc Furnace Flue Technology
Recent developments in electric arc furnace flue technology have focused on several key areas:
- Emission Control: Advanced filtration systems are now integrated into flue designs to capture particulate matter and toxic gases, ensuring compliance with environmental regulations.
- Heat Recovery: Innovative heat recovery systems allow for the reuse of waste heat, improving overall energy efficiency and reducing operational costs.
- Modular Designs: New modular flue designs facilitate easier installation and maintenance, allowing for quicker upgrades and adaptations to changing production needs.
- Smart Monitoring: The integration of IoT technology enables real-time monitoring of flue performance, allowing for predictive maintenance and enhanced operational efficiency.
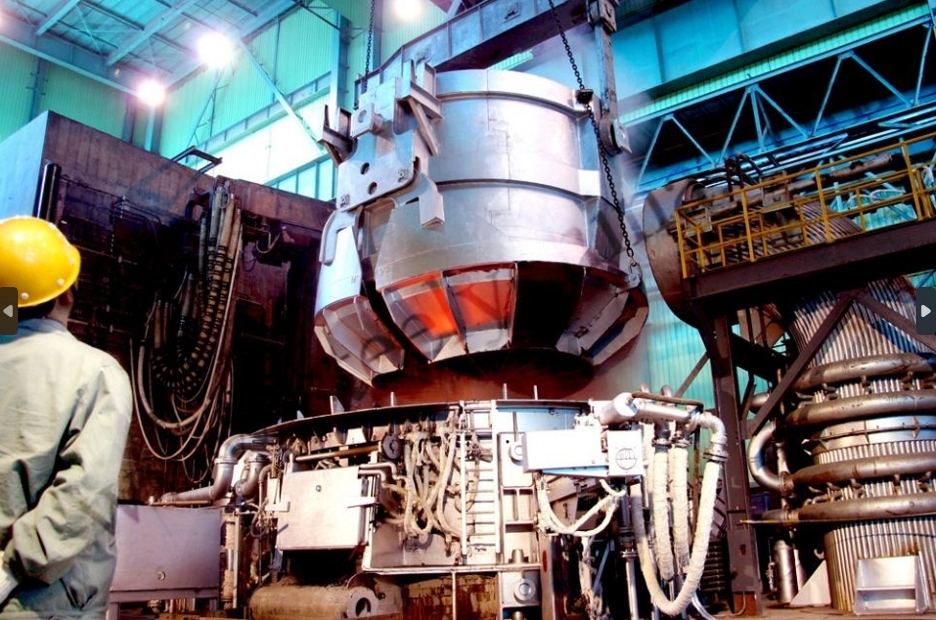
Benefits of Advanced Electric Arc Furnace Flue Systems
The implementation of advanced electric arc furnace flue systems offers numerous benefits:
- Reduced Emissions: By effectively capturing and treating emissions, these systems contribute to cleaner air and a healthier environment.
- Cost Savings: Enhanced energy efficiency and reduced waste translate into significant cost savings for manufacturers.
- Regulatory Compliance: Advanced flue technologies help companies meet stringent environmental regulations, avoiding potential fines and enhancing their reputation.
- Improved Safety: Effective gas management reduces the risk of hazardous conditions in the workplace, promoting a safer environment for workers.
Technical Specifications of Electric Arc Furnace Flue Systems
To better understand the capabilities of electric arc furnace flue systems, the following table outlines key technical specifications:
Parameter | Description | Value |
---|---|---|
Flue Diameter | Internal diameter of the flue | 500 mm – 1200 mm |
Material | Construction material of the flue | Stainless Steel / Carbon Steel |
Temperature Resistance | Maximum operating temperature | Up to 1200 °C |
Filtration Efficiency | Percentage of particulate matter captured | 95% – 99% |
Gas Flow Rate | Maximum gas flow rate through the flue | 1000 m³/h – 5000 m³/h |
Noise Level | Operational noise level | Below 85 dB |
Maintenance Interval | Recommended maintenance frequency | Every 6 months |
Weight | Weight of the flue system | 500 kg – 2000 kg |
Installation Time | Estimated time for installation | 1 – 3 days |
Warranty Period | Standard warranty period offered | 2 years |
Case Studies: Successful Implementations
Several companies have successfully integrated advanced electric arc furnace flue technologies into their operations, showcasing the benefits of these innovations:
Case Study 1: Steel Manufacturer A
Steel Manufacturer A implemented a new electric arc furnace flue system that reduced emissions by 30% while improving energy efficiency by 20%. The company reported significant cost savings and enhanced compliance with environmental regulations.
Case Study 2: Metal Recycling Facility B
Metal Recycling Facility B adopted a modular electric arc furnace flue design, allowing for rapid installation and maintenance. The facility achieved a 95% filtration efficiency, significantly improving air quality in the surrounding area.
Future Trends in Electric Arc Furnace Flue Technology
The future of electric arc furnace flue technology looks promising, with several trends emerging:
- Increased Automation: The use of automated systems for monitoring and controlling flue operations will enhance efficiency and reduce human error.
- Integration with Renewable Energy: Future designs may incorporate renewable energy sources to power flue systems, further reducing the carbon footprint of metal production.
- Advanced Materials: Research into new materials that can withstand higher temperatures and corrosive environments will lead to more durable and efficient flue systems.
Conclusion
Electric arc furnace flue technology is at the forefront of sustainable metal production. With ongoing innovations in emission control, heat recovery, and smart monitoring, these systems are essential for reducing the environmental impact of metal manufacturing. As the industry continues to evolve, the integration of advanced electric arc furnace flue technologies will play a crucial role in achieving sustainability goals and ensuring compliance with environmental regulations.
For more information on electric arc furnace flue systems and their applications, visit HANI TECH and explore their extensive range of metallurgical solutions.