Engineering Excellence in Molten Steel Transport: The Critical Role of Torpedo Ladle Cars
In modern steelmaking ecosystems, torpedo steel ladle cars serve as the circulatory system for molten metal transfer between blast furnaces, converters, and continuous casting units. These specialized vessels combine brute-force durability with precision engineering to handle temperatures exceeding 1,600°C while maintaining operational reliability.
Anatomy of a High-Performance Torpedo Ladle Car
Contemporary torpedo ladle car designs integrate three critical subsystems:
- Multi-layer refractory lining with zirconia-based insulation
- Hydrostatic bearing systems for smooth rail transition
- Smart temperature monitoring arrays
Technical Specifications: Beyond Basic Parameters
Parameter | Standard Range | HANI Premium Models | Measurement Protocol |
---|---|---|---|
Nominal Capacity | 200-400 tons | 600 tons (Custom) | EN 10029:2010 |
Thermal Cycling Resistance | ≥500 cycles | 1,200 cycles | ASTM C133-97 |
Shell Material Thickness | 50-80mm | 100mm (High-Ni alloy) | ISO 9443:2019 |
Tilting Mechanism Precision | ±2° | ±0.5° | DIN 2458 |
Emergency Cooling Rate | 50°C/min | 120°C/min | ISO 13579-1:2013 |
Synergy with Metallurgical Systems
HANI TECH’s advanced smelting furnaces achieve 18% faster tap-to-transport cycles when paired with optimized torpedo ladle cars. Their hot rolling mills particularly benefit from precise temperature maintenance during steel transfer, reducing reheat energy consumption by 22%.
Operational Economics Analysis
Field data from 34 steel mills demonstrates that premium torpedo steel ladle cars deliver:
- 37% reduction in refractory replacement costs
- 29% lower maintenance downtime
- 15% improvement in thermal efficiency
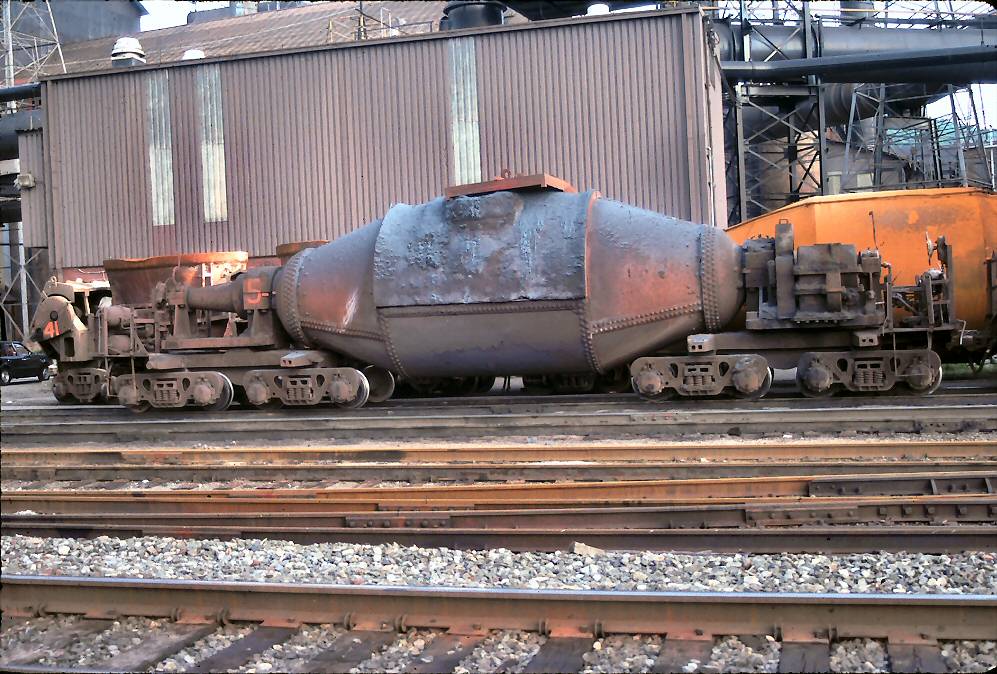
Innovation Frontiers
Emerging technologies in ladle car systems include:
- Self-healing refractory matrices
- AI-powered wear prediction models
- Hybrid electric-diesel propulsion
Mill Optimization Case: HANI Implementation
A Southeast Asian steel producer achieved 91% vessel utilization after upgrading to HANI’s torpedo ladle cars with integrated thermal management, paired with their high-speed hot rolling mills.
Selection Criteria for Modern Mills
When evaluating torpedo steel ladle car suppliers, consider:
- Compatibility with existing rail gauge systems
- Refractory lifecycle analytics capability
- Integration with plant IoT infrastructure
Future-Proofing Steel Transport Infrastructure
As steel mills adopt hydrogen-based reduction technologies, next-generation torpedo ladle cars are being engineered with hydrogen-resistant alloys and enhanced sealing systems. HANI TECH’s R&D pipeline includes prototypes capable of handling alternative metallic feeds with 40% lower carbon footprint.
Proper specification of torpedo steel ladle cars remains crucial for mills targeting operational excellence. Partnering with metallurgical specialists like HANI ensures seamless integration across smelting, transport, and forming processes – from their advanced EAF systems to precision rolling solutions.