Description
VD-type vacuum ladle refining furnace has vacuum degassing capability. VOD-type vacuum ladle refining furnace has the functions of decarbonization, deoxygenation, and dehydrogenation. It can produce a variety of stainless steel or ultra-low carbon alloy steel. In order to increase productivity.VD system can also be designed as a multi-vessel system.
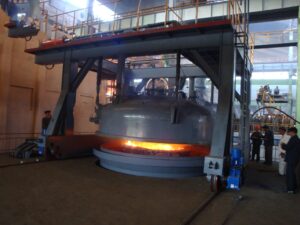
The main benefits of VD/VOD
1、Enhanced Reaction Velocity in Vacuum.
2、Improved steel cleanliness.
3、Achieving low contents of carbon/oxygen/hydrogen/nitrogen and sulfur.
4、Cost-Effective Investment.
5、Economical in Operating Costs.
VACUUM TREATMENT
Investment in steel vacuum degassing processes, both in new plants and upgrades of existing plants are continuing as steel companies see the opportunity to increase the value of their products by improving their quality and supplying more special steels.
For reasons of economy, these processes are usually conducted on large quantities of molten steel in very large plants, and consequently, very large vacuum pumping capacities are usually required. These processes are potentially very dirty with large amounts of metallic fines and oxide dust being generated.
EFFECTIVE VACUUM SYSTEM DESIGN
High-performance vacuum pumps are the heart of secondary metallurgical vacuum processes. Our vacuum pump technologies are tuned to your specific steel conditions and to your individual plant and production requirements.
Our vacuum pump systems precisely control the rate of pressure reduction from atmospheric level to low vacuum pressure. During the various treatment steps, the vacuum level is accurately controlled to match the system’s metallurgical needs.
To achieve optimal outcomes, our design incorporates essential elements such as high suction capacity, and low energy consumption, and optimal reliability.
VACUUM PUMP INTEGRATION
For VD, the necessary level of vacuum can be generated by conventional steam ejector pumps with steam ejectors installed alone or in combination with liquid-ring pumps allowing to save about 20% of steam consumption.
Recently, mechanical pumps are configured as a combination with liquid-ring pumps or screw compressors, regarded as dry mechanical pumps and Roots blowers have turned out to be an alternative. Of all advanced innovations, we have a proven record of success in many applications.
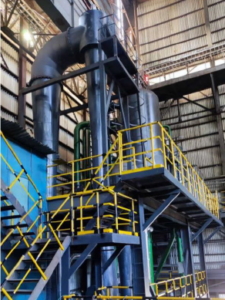
1. STEAM EJECTOR SYSTEM
In the manufacture of high-quality steel, the raw steel is treated under a vacuum. Multi-stage jet vacuum pumps are used to create and maintain
thevacuum.
The pumps used in the steel degassing process have the following principal duties to perform:
Rapid evacuation of the process tank to the required pressure.
Maintenance of vacuum while at the same time pumping outa large flow of inert gas
Immediate availability
Resistanttodust
Operationally safe even under the roughest conditions Steam ejector vacuum pumps are concentrated on the larger melt sizes mainly in integrated steel plants because of theiravailability of steam.
2. STEAM EJECTORS WITH LIQUID-RING PUMPS
Steam ejector systems have made progress regarding steam
consumption (save 20% approx.)by combination with liquid ring vacuum
pumps as primary stage. In many cases, this combination is advantageous
from an economic point of view.
Steam ejector pumps are mass conveyors and their suction capacity definition is done based on mass flow rates.
Mechanical pumps are pure volume conveyors, therefore the correct way of their suction capacity definition should be referred to the volume flow rates.
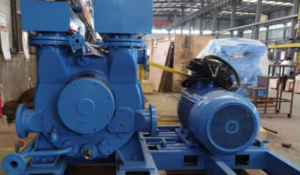
Liquid ring pumps are a very economical and reliable way to generate fast roughing and high-capacity backing for large sets of Rootsblower.
They are simple pumps for hogging and higher pressure processes (e.g.VOD) and have been a standard alternative for steam ejectors in these duties for many years.
They are inherently quite tolerant of process dust and dirts since these are largely absorbed and flushed out with the seal water.
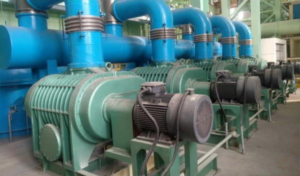
The dry mechanical pumps system, commonly have 3 or 4 stages using dry screw primary pumps, exhausting to the atmosphere and Roots pumps for the high-volume flow units.
The proven advantages of dry mechanical pump systems are mainly lower operational costs and push-button availability. Mechanical pump systems runs with minimum cooling water requirement and low energy consumption are also very attractive.