Description
1. Introduction to Hot Metal Tanks
A Hot Metal Tank (HMT) is a heavy-duty industrial vessel designed to store, transport, and pour molten metals such as iron, steel, aluminum, and copper at extremely high temperatures (typically 1,400°C–1,600°C). These tanks are crucial in industries like steelmaking, foundries, automotive manufacturing, and metal recycling, ensuring safe and efficient handling of liquid metal.
Key Functions of a Hot Metal Tank
- Storage: Maintains molten metal at optimal temperatures before further processing.
- Transportation: Moves liquid metal between furnaces, casting lines, and molds.
- Pouring: Enables controlled transfer into molds or refining vessels.
- Temperature Regulation: Minimizes heat loss for energy efficiency.
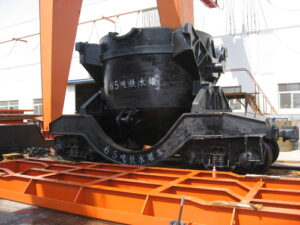
2. Design & Construction of Hot Metal Tanks
Hot metal tanks are engineered for durability, thermal resistance, and safety, incorporating advanced materials and structural features.
A. Core Components
Component | Material & Function | Importance |
---|---|---|
Refractory Lining | Made of ceramic, graphite, or alumina to resist extreme heat and chemical erosion. | Prevents tank failure from molten metal corrosion. |
Steel Shell | High-grade carbon steel or alloy steel for structural support. | Provides rigidity and impact resistance. |
Insulation Layer | Ceramic fiber, vermiculite, or calcium silicate to reduce heat loss. | Improves energy efficiency and worker safety. |
Lid & Sealing | Hydraulic or mechanical lid to prevent oxidation and heat escape. | Maintains metal purity and temperature. |
Tilting Mechanism | Hydraulic/pneumatic system for controlled pouring. | Ensures precision in metal transfer. |
B. Advanced Features
- Pre-Heating Systems – Gas or electric heaters to maintain temperature before filling.
- Thermal Monitoring – Infrared sensors and thermocouples for real-time temperature tracking.
- Slag Removal – Built-in slag separation for cleaner metal transfer.
- Emergency Cooling – Backup systems to prevent overheating risks.
3. Types of Hot Metal Tanks
Different industries require specialized HMT designs. Below are the most common types:
Type | Primary Use | Key Features | Industries |
---|---|---|---|
Torpedo Ladle Car | Transporting molten iron in steel plants. | Rail-mounted, long cylindrical shape. | Steelmaking |
Open-Top Ladle | Pouring metal into molds. | No lid, easy slag removal. | Foundries |
Tilting Furnace HMT | Melting and transferring metal. | Integrated tilting for precise pouring. | Aluminum smelting |
Mixer HMT | Blending different molten metals. | Large capacity, stirring mechanisms. | Metal recycling |
4. Industrial Applications
Hot metal tanks are indispensable in multiple high-temperature metal processes:
A. Steel Industry
- Blast Furnace to Converter Transfer: Moves molten iron to Basic Oxygen Furnaces (BOF).
- Ladle Metallurgy: Adjusts alloy composition before casting.
B. Foundries & Casting
- Sand Casting: Holds molten metal until mold filling.
- Die Casting: Supplies liquid aluminum for automotive parts.
C. Metal Recycling
- Scrap Melting: Recycles waste metal into reusable ingots.
D. Automotive & Aerospace
- Engine Block Production: Stores molten aluminum for precision casting.
- Turbine Component Manufacturing: Handles high-grade titanium alloys.
5. Key Specifications & Selection Criteria
When choosing a hot metal tank, consider:
Parameter | Standard Range | Selection Factors |
---|---|---|
Capacity | 5–100 tons | Production volume needs. |
Max Temperature | 1,400°C–1,800°C | Metal type (iron, aluminum, etc.). |
Lining Material | Alumina, Magnesia, Graphite | Chemical compatibility. |
Heating Method | Gas/Electric/Induction | Energy efficiency. |
Lifespan | 5–15 years | Maintenance & material quality. |
6. Maintenance & Safety Best Practices
To maximize hot metal tank longevity, follow these protocols:
A. Routine Inspections
- Refractory Wear Check – Cracks or erosion can lead to leaks.
- Thermal Imaging – Detects insulation failures.
- Mechanical Parts Test – Ensures tilting and sealing systems work.
B. Safety Measures
- PPE for Workers – Heat-resistant suits, face shields.
- Spill Containment – Drip pans and emergency cooling.
- Pressure Relief Valves – Prevents explosions from gas buildup.
8. Conclusion
A hot metal tank is a vital asset in metal production, casting, and recycling, ensuring safe, efficient, and cost-effective molten metal management. By selecting the right design, material, and capacity, industries can optimize workflow and reduce operational risks.
For custom hot metal cans, consult HANI tect, a leading manufacturer specializing in high temperature industrial solutions.